機械部品の知能化のための研究
機械部品は最も過酷な状況に晒されています。絶えず強い力が加わったり、摩擦や摩耗環境にさらされたり、高温下でも動作しなくてはなりません。
そうした部品を賢くすることで、部品自身が自分の限界を教えてくれるようになります。部品自体が賢くなると、システムや装置自体がより賢くなり、制御しやすく、機械や材料と人間とのコミュニケーションも向上します。また、部品が劣化した場合に、劣化した部分だけを修復する機能を有していれば、再利用可能な便利な部品も作ることができます。
ご興味ある方は、そのような夢の技術をいっしょに開発しましょう!!
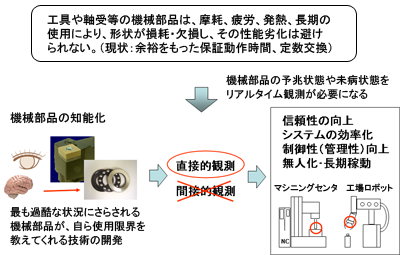
インテリジェント機械部品を用いたリモートメンテナンスシステム
機械部品の知能化技術(摩耗・欠損検知センサ付切削工具)に関する研究
図1. 摩耗・欠損検知センサ付切削工具
(第五世代の工具開発)
図2. 摩耗・欠損検知センサ付き切削工具と
ホルダーの取り付け例
図3. CVD切削工具コーティング
(第一世代から第四世代への変遷)
この研究において、摩耗量や欠損劣化が検知できるセンサが一体化された切削工具を開発し、これを用いた旋削用工具摩耗計測システムを開発しました(図1)。
摩耗センサ付切削工具は、セラミック母材上に切れ刃稜線に平行な数本の細線パターンをもつTiN製センサ薄膜が一体化された構造をもっています。細線は逃げ面摩耗の進行とともに断線するので、細線両端間の電気抵抗もそれに応じて不連続に変化します。
この不連続回数をメジアンフィルターを用いた信号処理により求めると、細線間隔の分解能で逃げ面摩耗幅が切削をしながらオンラインで知ることができます。
次に、逃げ面摩耗幅が測定できる機能を持った3-line型を開発しました。摩耗を検知するセンサは、ノーズRを取り巻くように切れ刃稜線と平行に置かれたいくつかの導電性細線で構成される部分です。細線は両端において平行結合されており、この両端の電気抵抗を加工中にモニタリングすると、逃げ面摩耗の進行に伴って細線が切れ刃稜線の近い部分から順次断線していくので、細線両端の電気抵抗もそれに応じて不連続に増加するものと考えられます。
この電気抵抗の不連続回数を、メジアンフィルターを用いた簡単なアルゴリズムによる信号処理により求めれば、それが断線した細線数に対応するので、既知の細線間隔の分解能で逃げ面摩耗幅をインプロセスで検知できます。
図2に、工具摩耗計測システム構成を示します。摩耗センサ付工具と座面上にコネクターピンをもった専用の工具ホルダー、デジタルマルチメータおよびパソコンで構成されています。マルチメータはコネクターピンを介して摩耗センサの電気抵抗を計測し、測定値はGB-IBを介してパソコンに送られて信号処理され、現在の逃げ面摩耗量や工具寿命限界の判断、チッピングの有無などが示されます。
図3に示したように、切削工具は第一世代から第四世代まで進展し、単層から多層膜とコーティングの膜の材料や構造を変化させて技術が向上してきました。本研究で開発したコーティング技術を活用した知能化は、新たな工具の方向性を示すもので、いわゆる第五世代の切削工具であると考えています。
機械部品の知能化技術(摩耗・はく離検知センサ付切削工具)に関する研究
図4. スラスト玉軸受
図5. スラスト玉軸受における劣化状態測定法の概念図
図6. 摩耗・はく離検知センサ付き軸受の寿命試験
軸受(ベアリング)は、摩耗、疲労、発熱、長期の使用などにより劣化することは避けられず、一般的には、あらかじめ設定された使用時間を超えた場合や、突発的に発生する損傷による動作不備が生じた場合に軸受の交換を行っています。
本研究では、スラスト型転がり軸受(スラスト型ベアリング)を例にして、スラスト型転がり軸受の軌道面上に、硬質で、かつ電気抵抗を検出可能にするセンサ構造を形成し、軸受動作中において損傷や劣化に関わる情報を物理量として直接的に計測する劣化検知センサ機能付きベアリングを開発しました(図4)。
スラストベアリングは軌道面の外輪、内輪ともに溝を有しますが、一方の溝を無くしてフラットにすると、面圧が増加し、溝がない方から欠陥が発生します。このため、センサ膜は軌道溝がない平板に作製して劣化状態を調べるようにすればよいのです。ここでは、汎用に使われている軸受鋼(SUJ2)を用いました。また、転導体に絶縁材料のSi3N4球を用い、かつ潤滑油も絶縁性の液体を使うことで、軌道面から転導体への電流漏れや電食の発生を防ぐようにしています。
図5では、並列にセンサ層の抵抗値を図る測定器が接続しています。スイッチの切り替えをおこなうことにより、あらかじめ配線しているセンサ部位の電気抵抗を測定します。軸受を回転動作させ続けていると、軌道面に堆積させたセンサ部において、摩耗やはく離などの現象が起こります。
このとき図5(a)のように、軸受(ベアリング)の動作をさせながらTiNセンサ薄膜の電気抵抗を測定することにより、摩耗現象により徐々にTiN層が次第に薄くなってきたり、断線したりするため、センサ薄膜の両端での電気抵抗値が上がっていく様子がわかります(図6)。
TiN層に電極をつけて約1mAの電流を流し、電圧降下からTiN層の抵抗値を求めることによって、軸受の損傷状態を判断するようにしました。軸受の疲労試験を行ってセンサ付き軸受の抵抗値の変化を求めたところ、図6の結果が得られました。これを見ると、 運転時間の経過とともにTiN層の抵抗値が増加しており、試験開始後は抵抗値が緩やかに増加していますが、軸受の劣化(摩耗やはく離)はほとんど起こっていないことがわかります。
そのため、若干の抵抗値の増加は軸受温度の上昇に因るものと考えられます。ある程度の試験時間を超えると抵抗値が急速に増加し、軸受の摩耗が進行していることがわかります。試験終了時には、図5のようにほぼ軸受の全周に渡ってTiN層が逸失した摩耗痕ができました。
このように、 単純な回路を構成し、TiN層に1mAの電流を流してその抵抗値を求めながら軸受の動作を行うことで、摩耗とはく離現象を区別しつつ、損耗の進行状態をインプロセスで計測することが可能となりました。なお、従来の間接的な計測である市販の振動センサを用いる手法もリファレンスとして同時に測定し、本システムとのデータとの相関をみており、直接的に測定する本手法の優位性が証明できています。